FOR IMMEDIATE RELEASE
NKC Releases Q1/2024 Milestone Progress Update on the Huygens™/ Proteus™ Technology
DATELINE: January 25, 2024, Los Angeles, CA
Neuro-KInesis, Corp. (NKC), is providing the following to share the revised milestone timeline for Q1 and Q2, 2024 as well as updates on the progress issues reported in the 2023 End-of-Year report released on December 29, 2023 in forwarding Neuro-Kinesis’ (NKC) development of its Huygens™/ Proteus™ Smart Catheter and Robotic Guidance System. The Huygens™ Catheter and the Proteus™ Robotic Arm are NKC’s lead product candidates for its line of SMART Surgical Tool technologies that combine advanced bio-data acquisition with enhanced Artificial Intelligence using proprietary micro-engineering and robotic-assisted control to provide surgeons an expanded tool-set to be able to deliver better surgical outcomes for their patients.
PROJECT MILESTONE UPDATE
NKC has released its revised calendar for Q1 and Q2 of 2024 to accommodate both the internal and external developments that necessitated a timeline adjustment for the Huygens™ Catheter milestones. As stated previously, NKC is working to move the development and testing of its unique electrophysiology (EP) mapping catheter to gather the data and validation studies as the company seeks Federal Drug Administration (FDA) approval for the next phase of in-human catheter testing.
To expedite the process of developing the Huygens™ Catheter for a clinical trial, NKC considered applying for a Humanitarian Device Exemption (HDE) by classifying the Huygens™ Catheter as a Humanitarian Use Device (HUD). The HUD/HDE application was designed as a pathway to expedite the approval of medical devices that meet the following conditions:
- The device is designed to treat or diagnose a disease or condition that affects fewer than 8,000 individuals per year in the U.S.
- The device is not available otherwise, and there is no comparable device available to treat or diagnose the disease or condition; and
- The device will not expose patients to unreasonable or significant risks, and the benefits to health from the use outweigh the risks.
NKC believes that its Huygens™ Catheter technology will provide a significant advancement to current state-of-the-art EP mapping catheter devices (See “Seeing the Forest From the Trees” – NKC Executive Summary and “What Lies Beneath the Surface” – NKC 2023 End-of-Year Report).
However, after reviewing the existing EP catheter technology on the market with the NKC regulatory consultant team of Dr. Elaine Duncan (Lead Regulatory Consultant) and Darci Diage (Manager of Regulatory and Quality Compliance), NKC has decided to pursue a more traditional 510(k) pathway for FDA approval.
The purpose of a 510(k) submission is to provide the FDA with documented evidence showing that a medical device is substantively equivalent in terms of safety and effectiveness to a predicate device. A predicate device is one that is already legally marketed and shares the same intended use and technological characteristics as the new device. The requirement is to compare the new device with the predicate by summarizing information from the design controls process, such as design features and verification testing. Currently, NKC is exploring using the St. Jude LiveWire™ Steerable EP Catheter as the predicate device it will be showing equivalency to.
ESTABLISHING A 510(k)
PRE-MARKET NOTIFICATION
The chart on the right shows the basic key points the FDA uses in determining if a submitted device meets the standards for safety and efficacy as the predicated device it being compared to.
Once submission has been made processing generally takes 30-90 days depending on the robustness of the initial application and any back-and-forth discussions that may occur.
Although the vision of the Huygens™ Catheter is to provide a consequential advancement in EP heart mapping ability, at its core the Huygens™ Catheter is an EP heart mapping catheter and meets all the requirements and standards of current predicate devices which already have FDA approval. By pursuing the 510(k) pathway, NKC believes it will have a much lower threshold to meet which should provide a more efficient and cost-effective course to gain certification to move forward with human clinical trials.
The 510(k) certification should also facilitate NKC’s secondary goal of submitting to the certified European Notified Body for Conformite Europeenne (CE) Mark certification for marketing and commercialization in the European Union (EU). The CE Mark assures that a product has met EU health, safety, and environmental requirements, which ensure consumer safety.
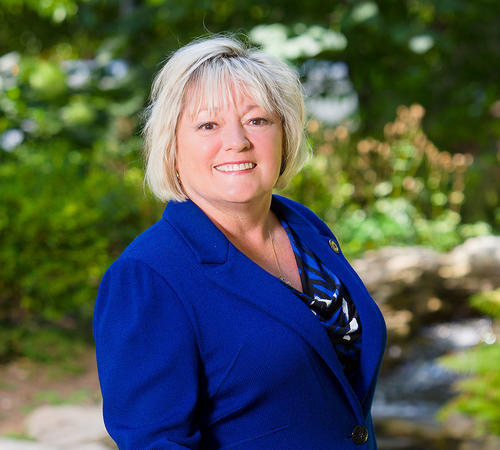
Helping to advance NKC’s regulatory strategy are Professor Elaine Duncan (on the left) and Darcy Diage (on the right). Professor Duncan is the founder and president of Paladin Medical®, Inc. and is a certified regulatory affairs professional with a master’s degree in engineering. She is a recognized leader in regulatory/clinical strategies for new medical technology development. Darcy Diage has more than 20 years of experience in evaluating risk assessment and commercial development activities for medical device technology interests. She assists in facilitating liaison relationships between NKC, the FDA, healthcare strategics, and other regulatory bodies to ensure timely and effective premarket review of NKC’s technology platforms by regulatory agents.
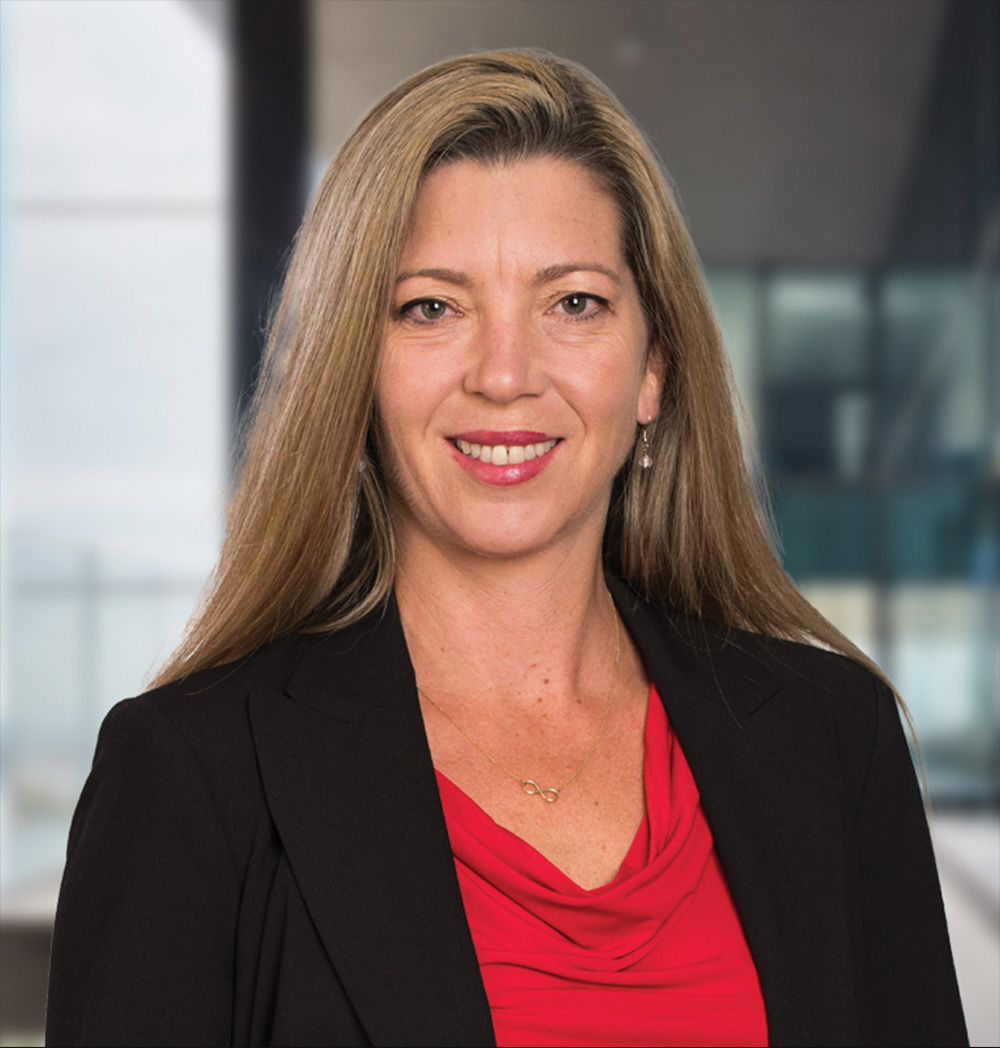
To meet these goals for submitting the Huygens™ technology for FDA and EU certification, NKC has set the following eight milestones that need to be met during Q1/24 that will move the validation data gathering forward to the Q2 and Q3 goals.
- Complete in-house verification testing of the Huygens™ Catheter prototype to all functional and performance requirements.
- Complete the assembly and testing of the Huygens™ Catheter electronic subsystems and submit the design specifications to a contract manufacturer for a pilot run.
- Complete the development of the Digital-to-Analog signal conversion (DAC) module to interface the Huygens™ Catheter’s digital output with the Ensite-X commercial mapping system.
- Refine the Proteus™ Robotic Arm User Interface (UI) and demonstrate cooperative control with the Huygens™ Catheter.
- Prepare documentation for a Phase I and II ISO 13485 Certification audit.
- Prepare all materials, documentation, and logistics to initiate the non-GLP Animal Study at the Harbor-UCLA Medical Facility in Torrance, California in Q2 2024.
- Prepare all materials and documentation for the safety certification audit of the Huygens™ Catheter by Intertek in Q2 2024.
- Prepare all materials and documentation for the second phase testing of the Huygens™ Catheter by Sandia National Laboratory in Q2 2024.
COMPLETE IN-HOUSE VERIFICATION TESTING OF THE HUYGENS™ CATHETER PROTOTYPE
The NKC Engineering team has been working to finalize all the initial design specifications for the electromechanical and firmware aspects of the Huygens™ Catheter. As was mentioned in the 2023 End-of-Year Report, all the initial modeling and testing of the technology had been completed on the bench-top Huygens™ Test Board, and the embedding of the firmware onto the actual proximal and distal flexible circuit boards (FCB) in the catheter tip for in-house catheter testing had begun.
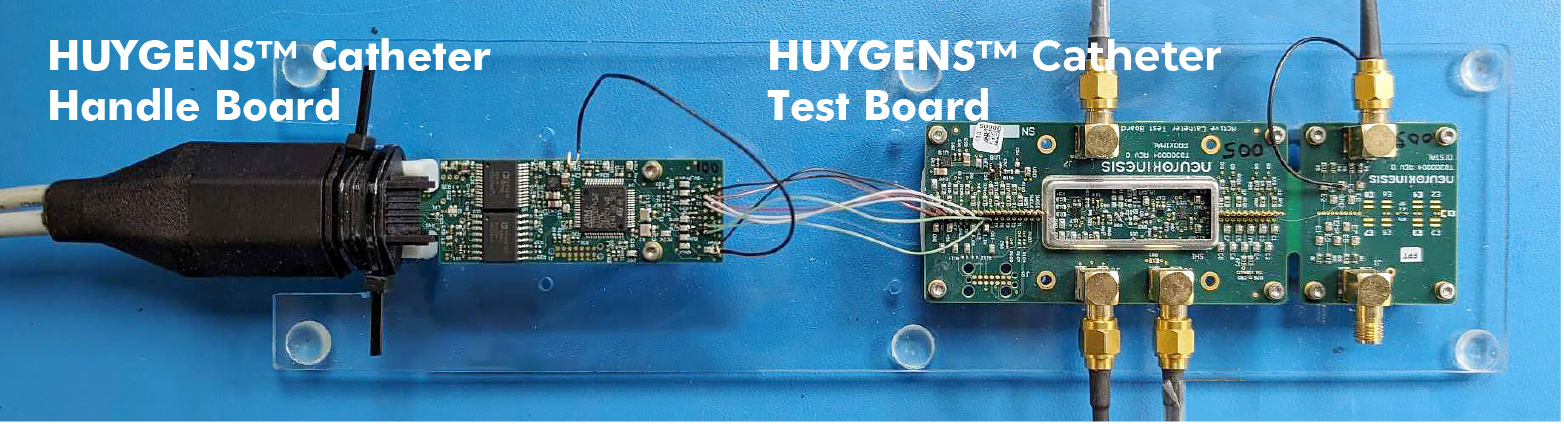
The image above shows the NKC Huygens™ Catheter Handle Board connected to the Huygens™ Catheter Test Board. The test board currently acts as a surrogate to validate communication between the catheter FCBs and the catheter handle board. In this test configuration, the handle board is connected to a PC which generates power to the catheter handle and the catheter FCBs via a USB connection. In the operating real-world environment, the handle board is connected to and powered by the Programmable Logic Controller (PLC). The PLC serves several important functions including regulation and delivery of power, navigation control, and system monitoring. The handle board also has a separate communication cable which sends the captured bioelectric signals made by the catheter to the EnSite mapping station which then creates the 3D heartmap.
As was stated in the last report, an issue arose in being able to transfer the firmware to the FCB and then power the FCB when connected to the Huygens™ Test Board. It was postulated that this problem was only an issue due to the attempt to power the FCB by the Huygens™ Test Board and that when the firmware-updated distal FCB was placed in configuration with the proximal FCB and the Huygens™ Catheter Handle Board as designed, the power issues would be resolved. It appears that this was the case and the team is now testing the completed power/data FCB configuration to make sure the electrode sensors and the signal processing and conversion to digital format for transmission to the EnSite Mapping station are operating to spec.
The NKC team hopes to have this aspect of the in-house testing completed by 01/25/24 so that the final design specifications can be made.
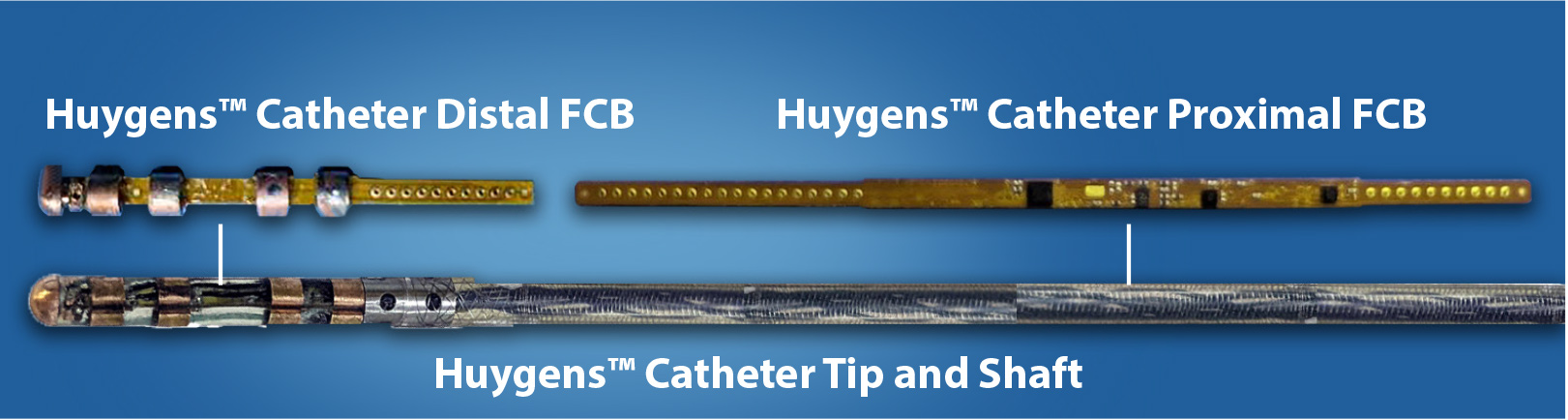
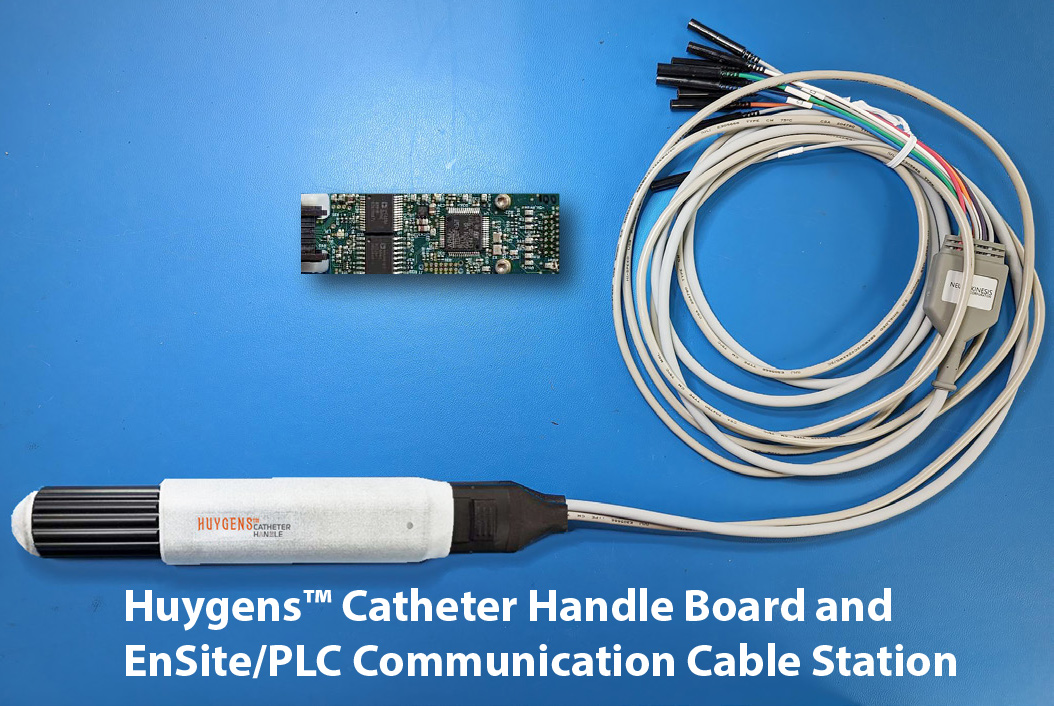
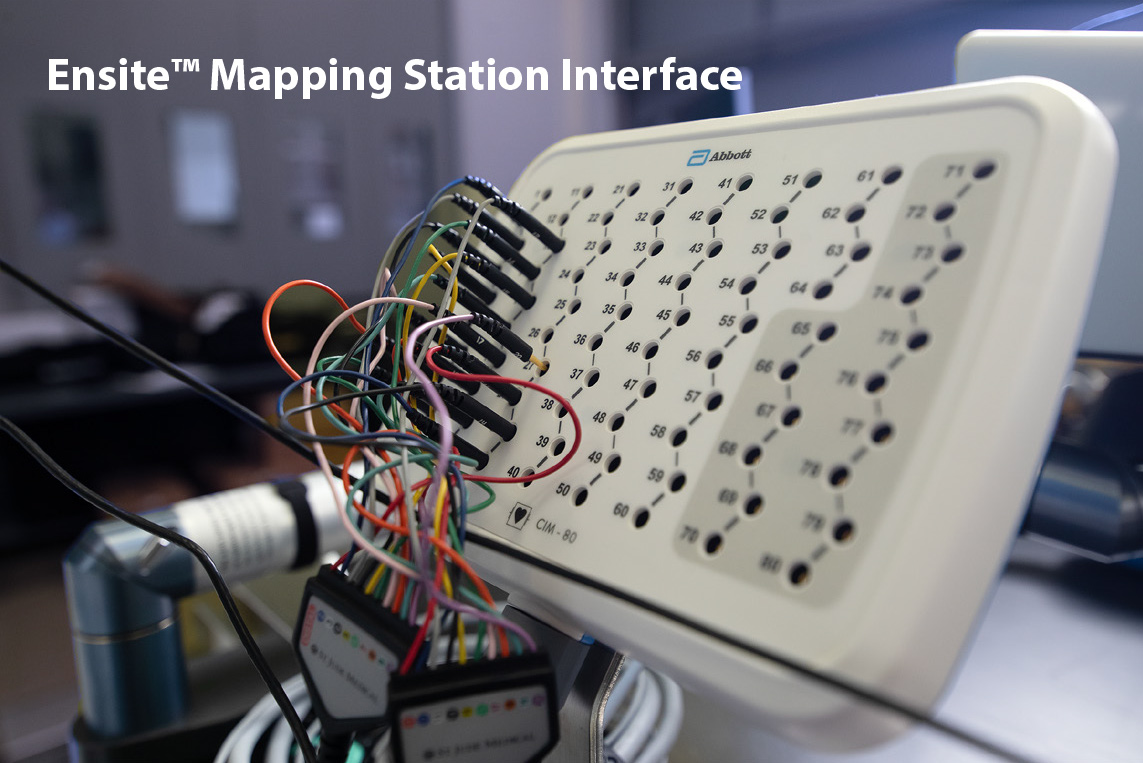
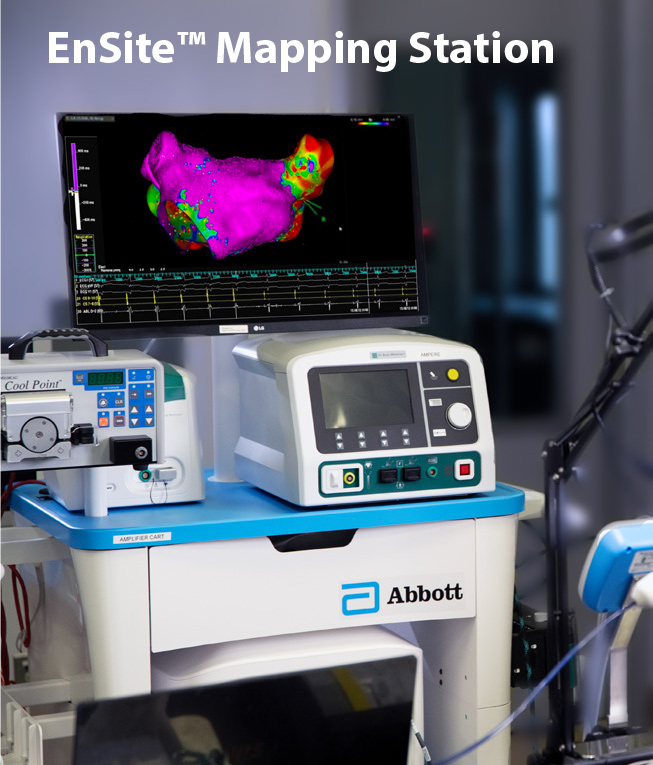
These images show how the communication pathways are managed between the Huygens™ Catheter and the Ensite mapping. The top left image displays the Huygens™ Catheter tip. The tip houses both a distal FCB which is where the bioelectric tissue measurements are captured from the nine electrode rings. These signals are then carried to the proximal FCB where they are amplified, and filtered. At this point, the signal is split into two channels. One channel is the analog transmission of the electrode readings for establishing the trilateration points, and the other channel is converted to an incorruptible digital signal which carries the biopotential and bioimpedance readings. Both of these signals are then sent to the Huygens™ Catheter Handle which is shown in the upper right image. The analog signal is transmitted to the multi-pin communication cable and the digital signal is transmitted to the digital connection cable. The digital signal is sent to the PLC and then to a Digital-to-Analog Converter (DAC) located near the mapping station to allow the signals to be converted to the analog signals needed by the Ensite Mapping station. All of the analog signals for both the trilateration positioning and the biopotential/bioimpedance measurements are then connected to the EnSite Mapping Interface shown in the bottom left image. With this information, the EnSite Mapping station is able to create the 3D EP heart map for the physician.
COMPLETE THE ASSEMBLY OF THE HUYGENS™ CATHETER SUBSYSTEMS FOR A PILOT RUN.
To be ready for the Q2 start of the initial non-GLP Animal Study for the verification, and safety testing of the Huygens™ Catheter technology, NKC will be manufacturing an initial run of five to ten prototypes of the Huygens™ Catheter. As had been discussed, NKC had submitted an RFQ from two leading medical catheter manufacturers in addition to the one they had received from SEISA Medical, which has partnered with NKC in the past. In addition to SEISA, NKC has approached Duke Emperical and Cath Concepts Development (CCD) who also have vast expertise in manufacturing medical catheters.
Duke Empirical, located in Santa Cruz, CA, is an ISO 13485-certified contract manufacturer that specializes in the design, development, and manufacturing of biomedical diagnostic catheters.
CCD is a global leader in the designing, rapid prototyping, and manufacturing of minimally invasive medical device components. CCD is based out of Plymouth Minnesota and offers a complete turn-key solution for all catheter development technologies as well as to provide services to their clients anywhere along their product’s life cycle. CCD and its highly skilled and motivated team focus on delivering fast, flexible, and innovative solutions with unmatched quality that meet ISO 13485, and international standards for device safety and functionality.
These quotes are currently under review.
Both a decision on the provider and the pilot production runs are in development so that prototypes will be in hand by March. Based on the testing of the first run catheters being able to perform to spec, NKC will be submitting a second run order for up to twenty-five more catheters that will be needed for both the Intertek Electro-Mechanical Compliance (EMC) study needed for ISO 60601-1 (See “PREPARE FOR INTERTEK SAFETY CERTIFICATION” below) and for the Phase II testing by Sandia National Labs (See “PREPARE ALL MATERIALS AND DOCUMENTATION SANDIA NATIONAL LAB STUDY”)
COMPLETE DEVELOPMENT OF THE DAC SIGNAL CONVERSION MODULE
One of the key features of the Huygens™ Catheter technology is its ability to acquire and process all bioelectrical signal capture at the catheter tip and then convert those signals to an incorruptible digital packet that can then be transmitted down the catheter shaft to the Huygens™ Catheter Handle and from there to an EP mapping station. This process all but eliminates issues associated with signal-to-noise acquisition and noise contamination by the current all-analog mapping catheters. NKC has finalized the ability to perform the analog to digital conversion at the FCB in the catheter tip to be able to send that signal to the Abbott/St. Jude EnSite mapping station.
NKC in 2022 had made a strategic partnership with Abbot/St. Jude to acquire the EnSite NavX as the mapping platform for the Huygens™/Proteus™ Technology. The EnSite NavX is currently considered to be the gold standard for EP 3D heart mapping. As the Ensite system was designed to work with existing analog catheters, the system’s interface uses an 18-wire proprietary analog connection array. To adapt to this, the NKC Engineering team is constructing a Digital to Analog (DAC) converter so that the biopotential measurements can be incorporated into the 3D heart map generated by the Ensite-X system.
As of this release, the team has completed the initial design and construction of the DAC module and has tested the system to successfully convert the Huygens™ digital signal to an analog signal on two channels which can then be read by the EnSite NavX. The team is now expanding the firmware to be able to convert the digital into the eight channels needed for the Ensite system.
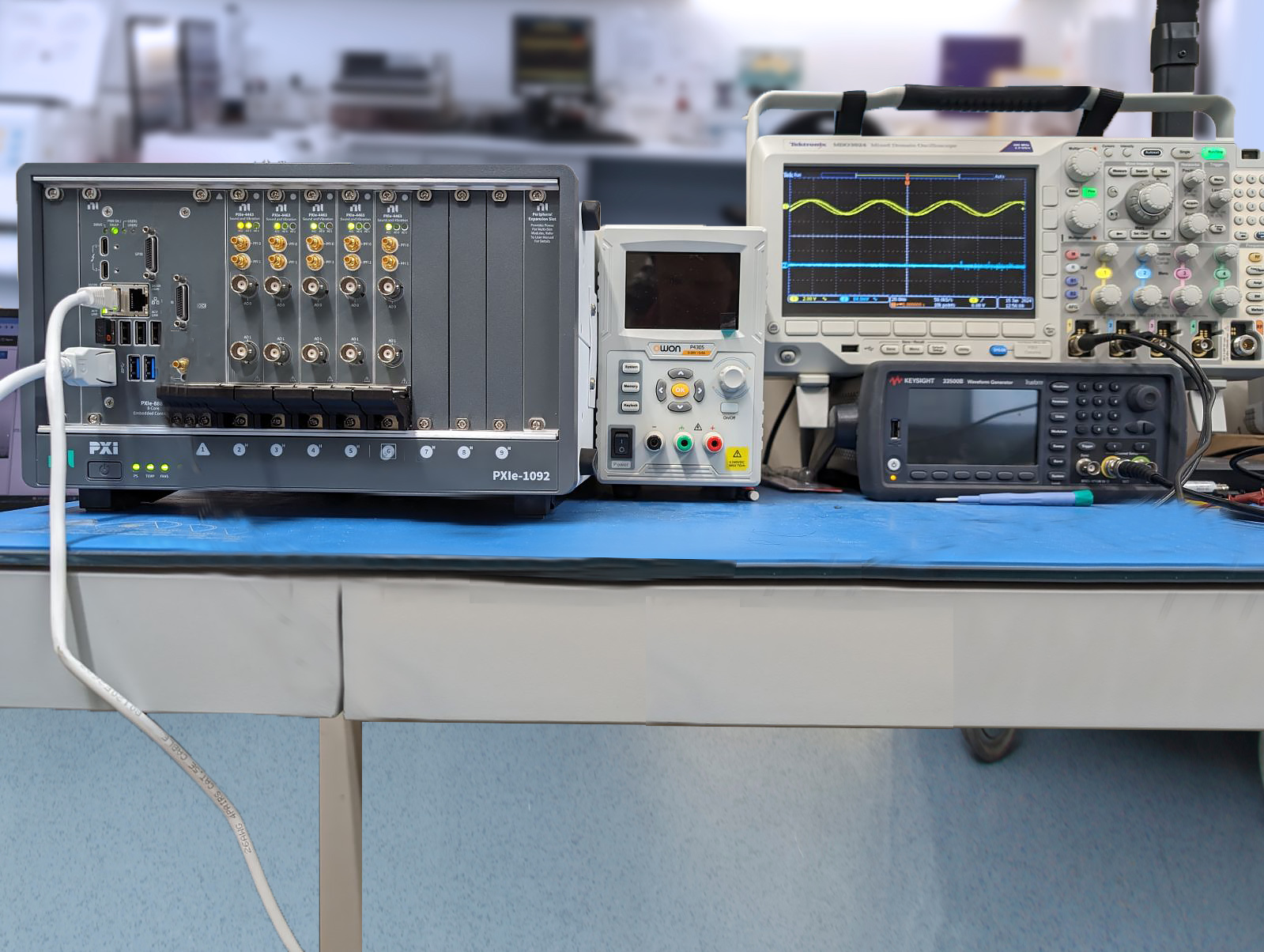
The image above shows the testing and simulation setup for the development of the DAC Control Module that will take the digital data stream from the Huygens™ Catheter and convert it to eight channels of analog information which are then fed to the EnSite Mapping Station for biopotential and bioimpedance mapping.
REFINE THE PROTEUS™ ROBOTIC ARM USER INTERFACE (UI)
Over the past several releases we have discussed the advancements made with the NKC Proteus™ Robotic Arm catheter navigation platform. The Proteus™ Robotic Arm is part of NKC’s innovative efforts to bring robotic-assisted AI technology to EP catheter navigation. The Proteus™ Robotic Arm is capable of fine-grain granular control of an EP catheter in any axis of direction. The system allows rotational motion in either a clockwise or counterclockwise direction through 180 degrees, as well as deflection and translation guidance with variable speed proportional response advancements as small as 1.5mm at a speed of up to 10mm per second. Control of the Proteus™ is accomplished by the EP surgeon via an advanced controller at the navigation station as well as autonomous AI guidance of programmed routines that can be performed by the navigational software. Although designed to work specifically with the NKC Huygens™ Catheter, the Proteus™ Robotic Arm will also be able to control navigation of any EP catheter that uses a comparable catheter steering handle.
In 2020 NKC completed the first phase of development with the Proteus™ I Robotic Arm. The Proteus™ I validated the ability to miniaturize all the electromechanical requirements of an advanced catheter navigation system by reducing the company’s 9-ton CGCI navigation operating suite into a portable shoe-box-sized plug-and-play system.
In 2023, NKC introduced the Proteus™ II as the next phase of development for the technology. With the Proteus™ II, the team is now working to integrate robotic control and artificial intelligence (AI) to bring both real-time Human-in-the-loop (HITL) capabilities and autonomous robotic catheter mapping navigation to reality.
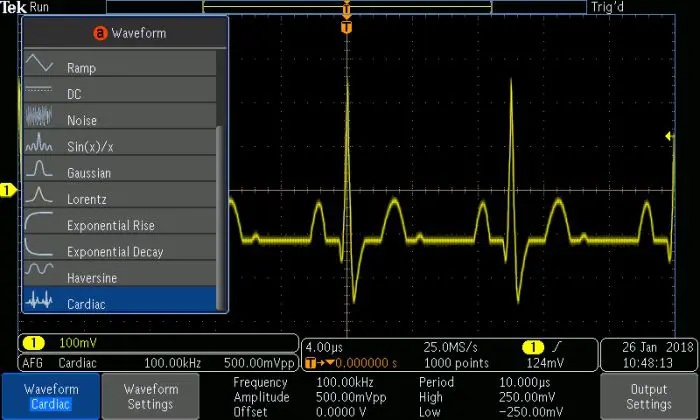
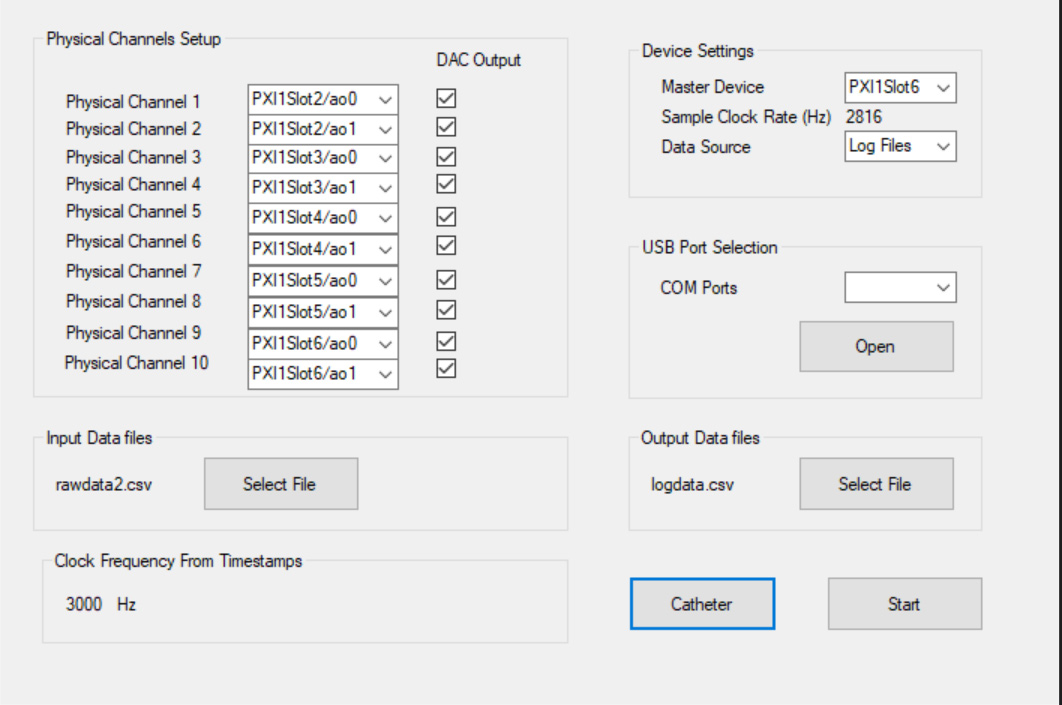
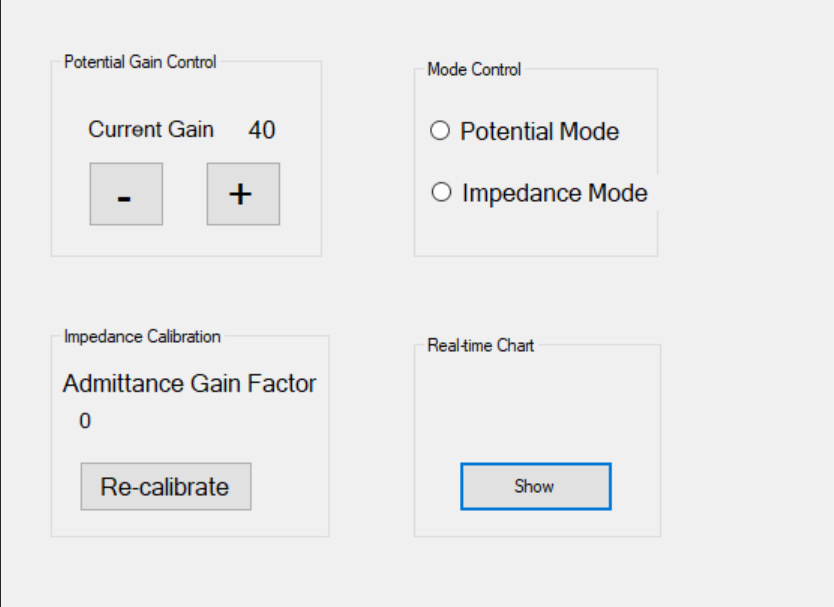
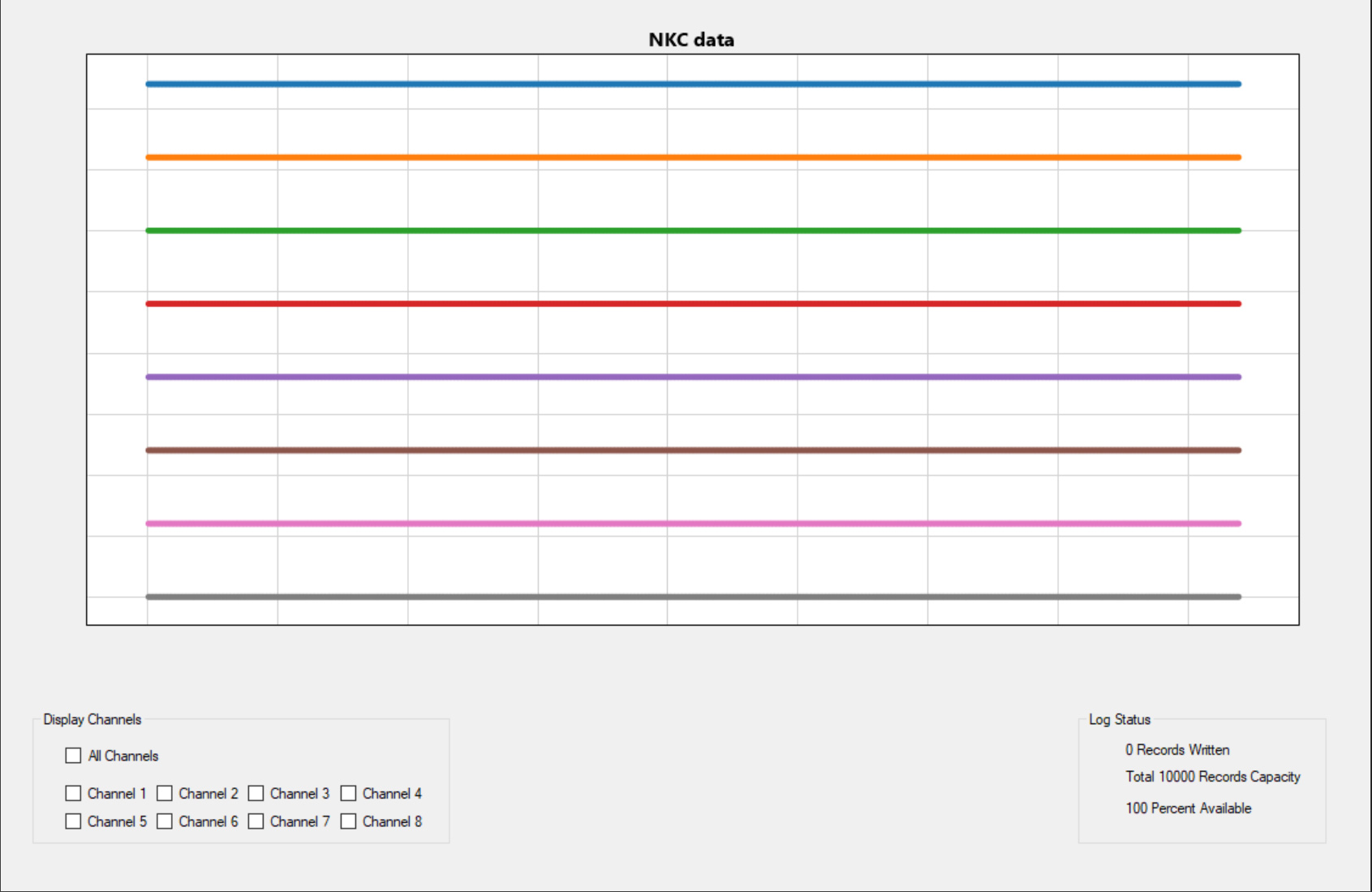
Current development of the DAC User Interface (UI) allows the system to receive and process a signal from the Huygens™ Catheter or a simulated signal from a source generator during testing. In this example, a generated QRS signal is sent to the DAC. The top left image shows this signal on an oscilloscope. The top right image shows the UI which allows the operator to select which channels they want to convert as well as some global system settings. The bottom left screen shows the UI that allows the operator to adjust the gain and calibration sensitivity of the catheter for both biopotential and bioimpedance readings. The bottom right screen will then display the converted digital signal that has been split into the various analog channels for the EnSite mapping station.
Last month, NKC shared the initial completion of the prototype Gripper for the system. The Proteus™ Gripper, which is mounted on the end of the robot arm, is designed to work with the Huygens™ Catheter and any other commercial steerable catheter with ring-based deflection control. The Gripper integrates with the Proteus™ Robotic Arm and Navigation Station to perform gross and fine-grain transmitted movements from the EP physician operator or the navigation computer, for all translational, rotational, and tip deflection movements.
In the 2023 End-of-Year Report we shared how during initial deflection testing, the team found that excessive torque buildup was occurring between the deflection ring and the clamp when the tip was moved beyond 15O of angle. This caused the handle to slip in the housing. As can be seen in the images to the right, the team has been able to modify the design which both provides a more secure grip to the catheter, as well as prevents slipping of the deflection ring during rotation.
As of the 2023 End-of-Year Report, the NKC team successfully implemented the software to enable the base functions for the Proteus™ II Robotic Arm. These included:
- A brake test for force and position calibration.
- A ready position mode to bring the robot arm into position for interfacing with the catheter.
- A COBOT mode which enables the physician to manually position the arm so that the Huygens™ Catheter can be loaded into the Gripper.
- Operational mode, which enables fine-grained control of the catheter tip position from a control console joystick.
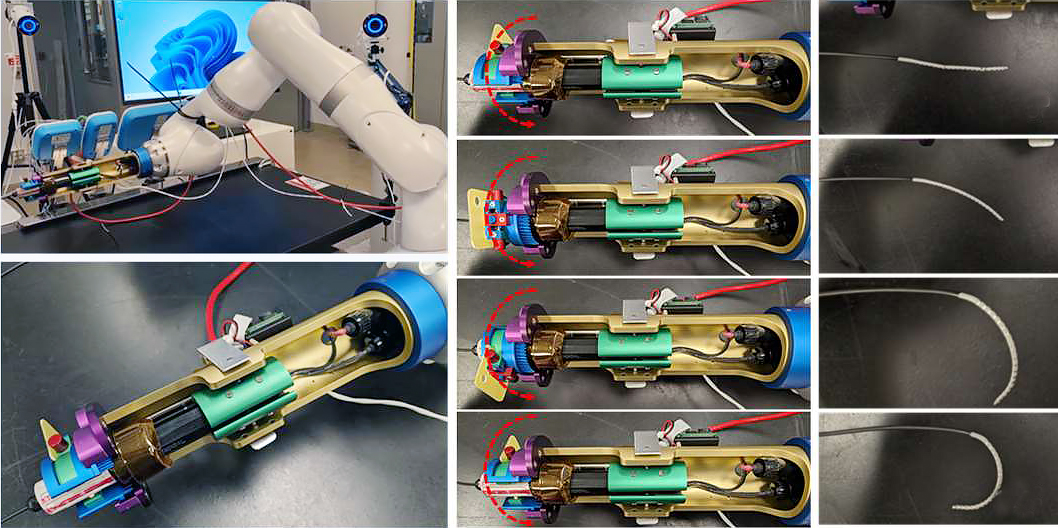
The images to the left show the Proteus™ Robotic Arm with the Gripper attached undergoing navigational testing for translational, rotational, and deflection control. As can be seen, the NKC Engineering team was able to modify the catheter lock-down assembly and the deflection ring gear control to eliminate any slippage or unwanted torque movement to the catheter handle during deflection. The images on the right show that full deflection of the catheter tip from 0o to 140o has been achieved. The modifications are now being redesigned for a final part configuration which will be incorporated in the next prototype run.
Last month, NKC shared the initial completion of the prototype Gripper for the system. The Proteus™ Gripper, which is mounted on the end of the robot arm, is designed to work with the Huygens™ Catheter and any other commercial steerable catheter with ring-based deflection control. The Gripper integrates with the Proteus™ Robotic Arm and Navigation Station to perform gross and fine-grain transmitted movements from the EP physician operator or the navigation computer, for all translational, rotational, and tip deflection movements.
In the 2023 End-of-Year Report we shared how during initial deflection testing, the team found that excessive torque buildup was occurring between the deflection ring and the clamp when the tip was moved beyond 15O of angle. This caused the handle to slip in the housing. As can be seen in the images to the right, the team has been able to modify the design which both provides a more secure grip to the catheter, as well as prevents slipping of the deflection ring during rotation.
As of the 2023 End-of-Year Report, the NKC team successfully implemented the software to enable the base functions for the Proteus™ II Robotic Arm. These included:
- A brake test for force and position calibration.
- A ready position mode to bring the robot arm into position for interfacing with the catheter.
- A COBOT mode which enables the physician to manually position the arm so that the Huygens™ Catheter can be loaded into the Gripper.
- Operational mode, which enables fine-grained control of the catheter tip position from a control console joystick.
During initial testing, the team observed two problems. The deflection of the catheter tip was limited to 15⁰, and the deflection speed was well below the target of 30-40⁰ per second required for practical use in an EP mapping procedure. By modifying the gear mechanism, adding clamps to reduce slippage during operation, and increasing power to the joystick, the team was able to achieve the full 140⁰ deflection in 3-4 seconds using a commercial Livewire Cather from Abbott.
Although the Proteus™ II Robotic Arm is not part of the initial animal study, nor is it tied to the Huygens™ FDA development path, the NKC team continues to pursue an aggressive path of development for the system. It is hoped that by the end of Q1/24 the next phase of firmware and UI development will be complete.
In addition, the team has also begun research into determining what its final physician controller needs will be. Currently, the team is looking at a variety of different controller types such as simple joystick, 3D Haptic controllers, trackballs, and others to determine what will work best for the system. The team will be working closely with NKC’s Chief Medical Officer, Dr. Eli Gang to gather input from several EP surgeons on what their current preferences are, what better ergonomics and control they would like to see, and what advancements in HITL navigation could be addressed to provide intuitive real-time, zero-latency control of a catheter inside the living dynamic of the human heart.
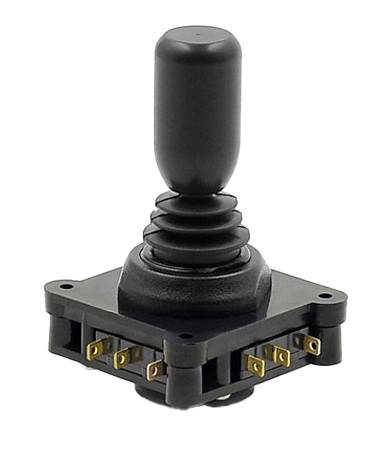
Finger Controller
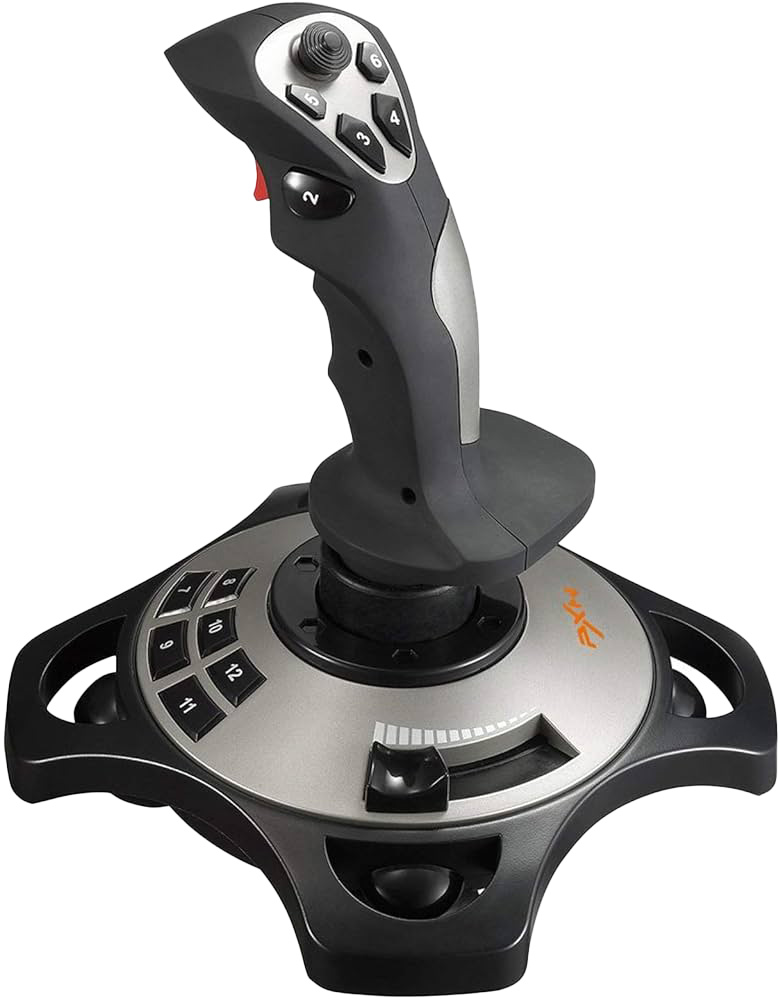
Flight Controller
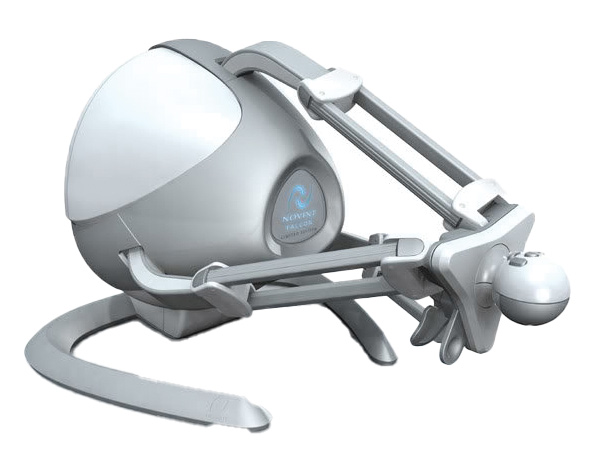
Haptic Controller
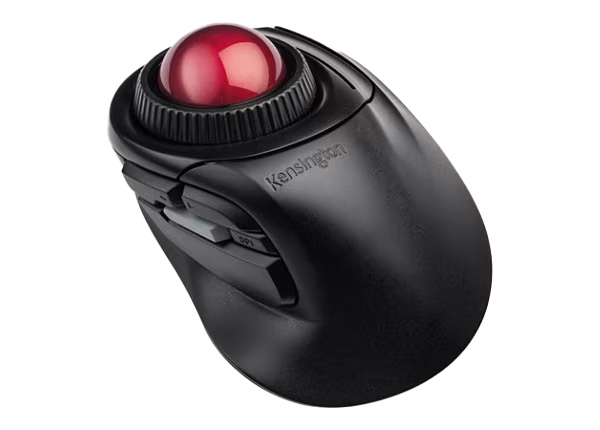
Trackball Controller
The NKC Engineering team is investigating final options for the user navigational control mechanism which will allow the EP physician or control operator to maneuver the Proteus™ Robotic Arm in 3D space. The goal is to find a controller that easily mimics the intuitive movements an EP physician would want to have for controlling catheter positioning in real time. The team is working with Dr, Eli Gang to gather feedback responses from other leading EP physicians to make an initial determination for control options to test out. Shown above are four of the most common types of navigational control types currently in use in medical tool operation.
PREPARE DOCUMENTATION FOR A PHASE I AND II ISO 13485 CERTIFICATION AUDIT.
NKC is preparing all the documentation required to achieve an ISO 13485 certification for its technology development. The ISO 13485 specifies the requirements an organization needs to demonstrate that its Quality Management System (QMS) has the ability to provide product development, documentation, manufacture, procurement, and distribution services that consistently meet consumer and applicable regulatory requirements.
The ISO 13485 is a globally recognized standard that helps organizations be accepted and recognized as safe and compliant within the industries they operate. The certification enhances an organization’s ability to consistently deliver safe and effective medical devices while fostering customer confidence and satisfaction. Additionally, adherence to ISO 13485 can open doors to international markets, as many countries require or recognize the standard as a benchmark for quality management in the medical device sector. Ultimately, ISO 13485 is a strategic tool for organizations committed to producing high-quality medical devices and ensuring patient safety.
To achieve this, the pursuing company must document and prove through both a Phase I and Phase II audit that they have met the needed criteria in the following areas:
- QMS Requirements: The pursuing company has established a QMS that meets the standard set by the ISO 13485. The QMS shows documented policies, procedures, and processes necessary for the effective planning, operation, and control of the organization’s activities related to its device technology. Further, the QMS defines the roles, responsibilities, and authorities of top management about the QMS. This includes demonstrating leadership, ensuring the availability of resources, and promoting a culture of quality.
- Regulatory Compliance: The pursuing company can demonstrate it has aligned its development, production, and management systems with regulatory requirements for its device technology in the various jurisdictions in which the ISO 13485 is recognized including the U.S. Food and Drug Administration (FDA) in the United States, the European Medicines Agency (EMA) in Europe, and other global regulatory bodies.
- Product Realization: The pursuing company has established a documented process and strategy that provides guidelines for the entire product realization process, including design and development, purchasing, production, installation, servicing of medical devices, and post-market activities. In addition, they have established processes related to all planning, risk management, verification, and device validation.
- Traceability and Documentation: The pursuing company has created an orderly and organized system for maintaining traceability throughout the product life cycle. This involves documenting and controlling changes, ensuring the integrity of the quality management system, and enabling the tracking of devices from production to end-user.
- Continuous Improvement: The pursuing company has a written procedure for its ongoing, systematic efforts to enhance the effectiveness and efficiency of its processes within its QMS. The procedure should promote a culture of continuous improvement by requiring organizations to monitor and measure their processes, assess customer feedback, and implement corrective and preventive actions. This ensures that the QMS remains effective and adapts to changes in the industry and regulatory landscape.
ISO 13485 CERTIFICATION
The ISO 13485 Certification establishes a company’s ability to meet the quality control and systems management processes that ensure reliability, safety, and accountability for a manufacturer, their consumers, and their employees. The process entails a very rigorous analysis of a company’s current policies to determine where it needs to modify them in light of current and future growth projections to make sure a level of high-quality production and management can be maintained. The chart below shows the various steps a company goes through in its process of seeking ISO 13485 Certification. NKC is very close to being ready for its Phase I audit.
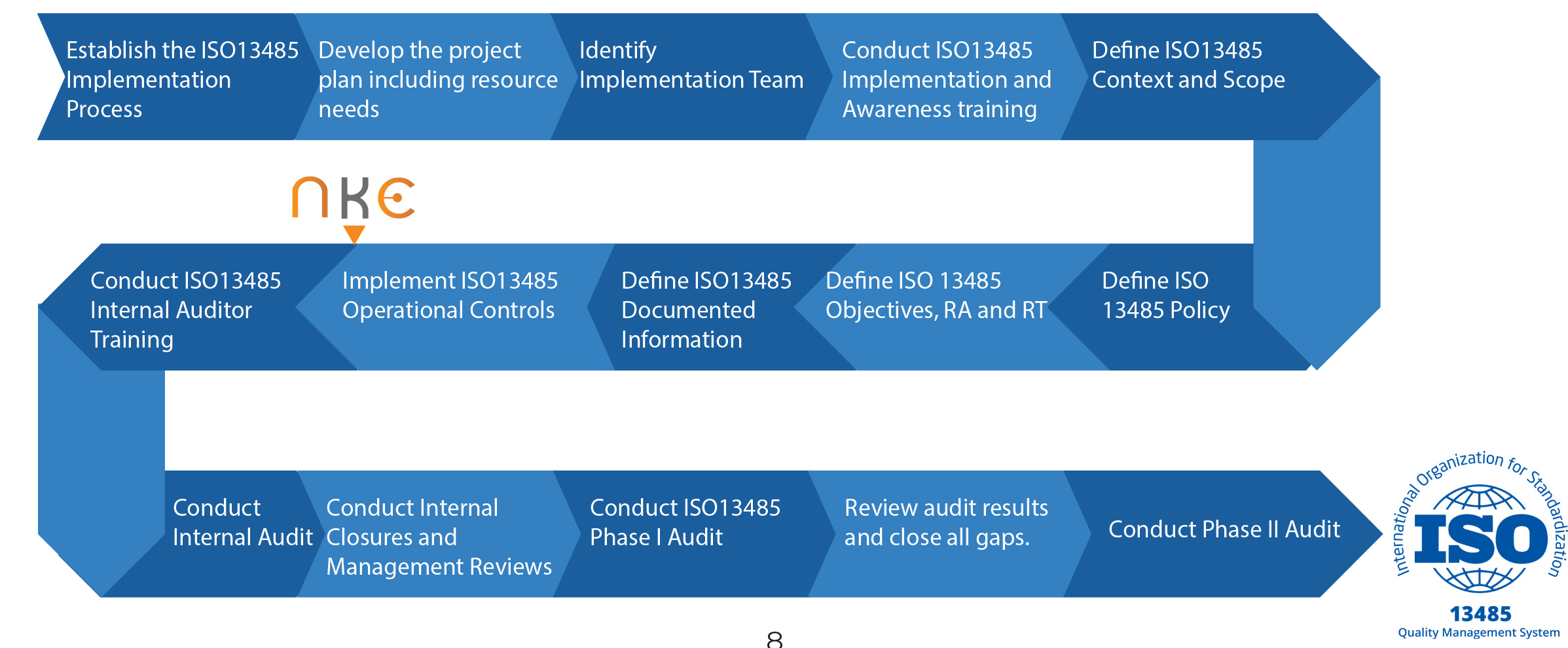
The NKC QMS team to date has already developed 79% of the documentation required for the Phase I audit covering design, production, tracing, and safety. In the 36 documents already released, the team has established its procedures for document control, vendor purchasing accounting, part traceability, staged product pipeline, and the user requirements for the Huygens™ Catheter and the Proteus™ Robotic Arm.
To support this, all engineering and related personnel have been trained on to manage their Design History File (DHF) process. DHF is a critical component within the QMS that provides a comprehensive history of the design and development activities associated with specific devices. The purpose of the DHF is to demonstrate that a device has been developed in accordance with the regulatory requirements and the organization’s own procedures. The DHF tracks all changes related to the following:
- Design and Development Planning: Documentation outlining the planning activities associated with the design and development of the device including project plans, timelines, and resource allocation.
- Design Inputs: Specifications, requirements, and criteria that define the intended use, features, and performance of the device.
- Design Outputs: Documents and records that demonstrate how the design inputs were transformed into tangible design solutions. This may include drawings, specifications, and other technical documentation.
- Design Review Records: Documentation related to formal reviews conducted at various stages of the design process. These reviews assess the progress, adequacy, and conformity of the design with established requirements.
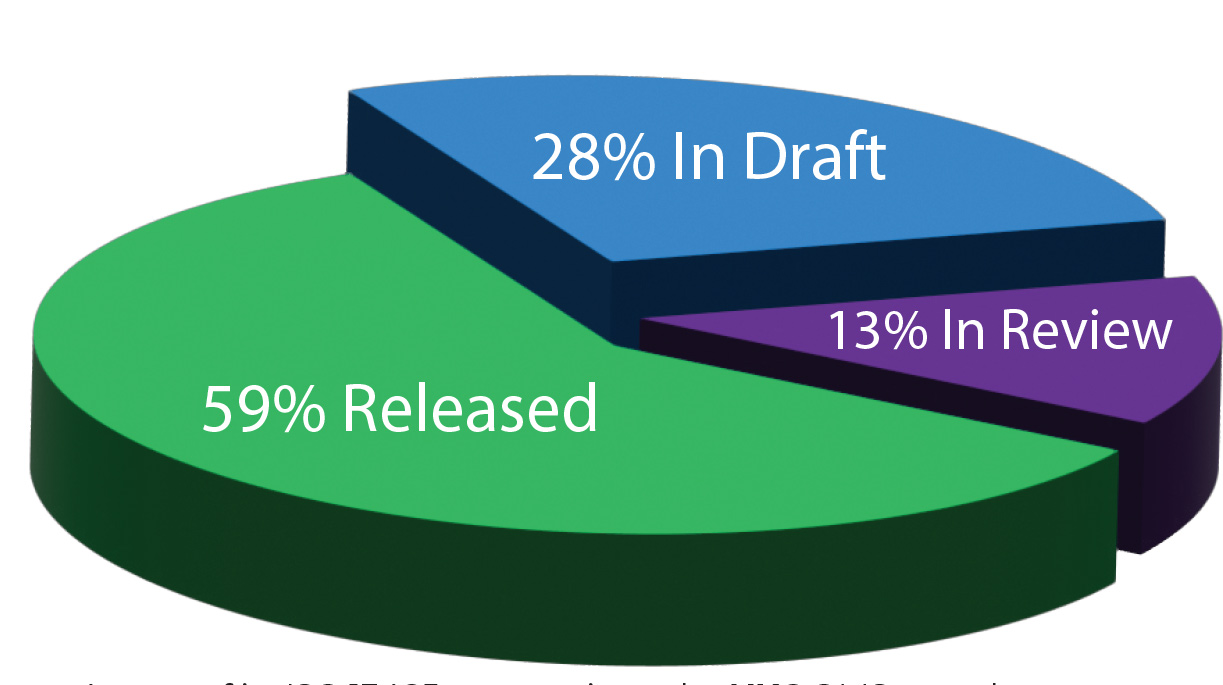
As part of its ISO 13485 preparations, the NKC QMS team has begun the development of a stringent Quality Management System (QMS) covering all aspects of technology research, development, procurement, manufacture, and testing protocols. The graph above shows where the process of documentation development stands.
MEDICAL DEVICE DESIGN CONTROL CYCLE
In constructing an effective DHF process, ensuring a proactive design control cycle is critical to success. Design controls describe an iterative, phase-gated design process that ensures regular reviews of a project’s progress against inputs like user needs, technical specifications and regulatory standards. It provides for the verification of designs against captured design requirements, and the validation of the finished product against user needs.
- Verification and Validation Activities: Records of activities confirming that the design meets specified requirements (verification) and that the final product performs as intended in its intended environment (validation).
- Design Changes: Documentation of any changes made to the design during the development process. This includes the rationale for the changes, verification, and validation of the changes, and any impact on other aspects of the design.
- Risk Management Documentation: Records related to the identification, assessment, and mitigation of risks associated with the medical device. This is crucial for ensuring that potential risks are adequately addressed throughout the design process.
- Design Transfer to Production: Documentation demonstrating the seamless transition of the design to the production phase. This includes any required information, training, and validation activities for manufacturing.
- Device Master Record (DMR): The Device Master Record is often included as part of the DHF. It compiles all the documentation necessary to produce, test, and distribute the medical device, providing a comprehensive record for production.
- Design History File Index: A master index or table of contents that outlines the structure and location of each document and record within the DHF. This facilitates easy navigation and retrieval during regulatory audits or inspections.
The balance of the documentation still to be finalized for the Phase I audit is centered around the various Inspection methods and test protocols that must be defined. NKC plans on having all certification policies, documents, and procedures in place by the end of Q1, 2024. At that point, NKC will apply for and schedule its Phase I audit. Although audit times can vary, typically the Phase I audit is scheduled within 30 to 45 days after filing. The primary purpose of the audit is to assess the organization’s preparedness for the full ISO 13485 certification audit. The audit can last from one to three days and is focused on the documentation and readiness review for the Phase II audit.
After the Phase I audit, NKC will address any concerns or changes brought out during the Phase I audit, and then the final Phase II audit will be scheduled. The Phase I audit is typically shorter in duration compared to Phase II. The Phase II audit is the main certification audit where the auditor evaluates the implementation and effectiveness of the organization’s QMS against ISO 13485 requirements. This audit involves on-site verification and may include interviews with personnel, observations of processes, and a review of records. Phase II audits are typically more extensive and can last several days. The exact duration depends on factors such as the organization’s size, complexity, and the number of processes and sites to be audited. Smaller organizations may have shorter audits, while larger and more complex organizations may require a more extended audit period.
NKC anticipates being able to complete the audits and be granted ISO 13485 certification by the end of Q2/24.
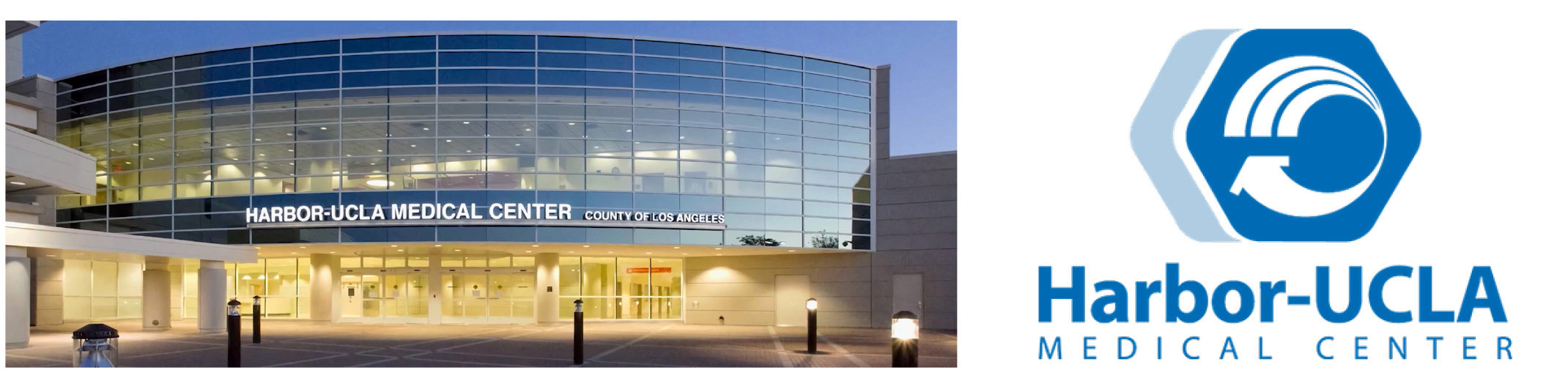
PREPARE MATERIALS AND LOGISTICS FOR THE NON-GLP ANIMAL STUDY
For the past year, NKC has been providing updates on its first non-GLP animal study of the Huygens™ Catheter. The animal study will be looking to gather data on all the various functions of the Huygens™ Catheter including the ability of the catheter to capture, process, and transmit bioimpedance and biopotential data to the EnSite mapping system to produce an accurate heart map in comparison with the existing art.
As was explained in the last release, the study which had been planned to begin on January 1 of this year at the Technion Institute in Haifa, Israel, had to be postponed because of the unforeseen conflict that arose in that part of the world. As a result, NKC quickly shifted gears and was able to set up the study to be performed at the Harbor-UCLA Medical Facility in Torrence, California. The dedicated 20,000-square-foot research lab fully meets the needs of the NKC initial study and has required very few changes to be made to the protocol document that had been developed for the Technion study.
The NKC Management team along with the Engineering team, Dr. Eli Gang, the study’s director, and Professor Elaine Duncan, NKC’s regulatory affairs consultant, are finalizing all the procedures, materials, equipment, and logistic planning for the study which is now scheduled to begin in the first part of Q2/24. This study is fundamental to NKC’s efforts for 510(k) approval by the FDA.
The NKC Management team has already begun planning and protocol design for the GLP study which will follow the successful completion of this first trial. The GLP study will be conducted to demonstrate “reasonable assurance of the safety and effectiveness of the device” as it relates to the 21 CFR Part 861 requirements for all Class II medical device manufacturers. These include:
- Device Classification: Outlines procedures and criteria for the classification of medical devices into different classes (Class I, II, or III) based on their intended use, indications for use, and the level of regulatory control deemed necessary for ensuring safety and effectiveness.
- Reclassification: Provides the process for reclassifying certain medical devices when new information becomes available or when the FDA determines that a change in classification is necessary to ensure the safety and effectiveness of the device.
- Rescission of Classification: Addresses circumstances under which the FDA may rescind the classification of a medical device. This typically involves situations where the FDA determines that a device is no longer appropriately classified.
- Effective Date of Requirement for Premarket Approval: Includes provisions related to the effective date for the requirement of premarket approval for certain Class III medical devices. Premarket approval is a regulatory process that evaluates the safety and effectiveness of high-risk medical devices before they can be marketed.
- Exemption from Premarket Approval: Discusses conditions under which a device that would otherwise require premarket approval may be exempted from this requirement.
- Special Controls: Allows for the establishment of special controls, including performance standards, post-market surveillance, patient registries, and other measures to provide adequate assurance of the safety and effectiveness of certain medical devices.
MEDICAL DEVICE CLASSIFICATION
In the US, medical devices are regulated by the FDA and are divided into three major classes with some sub-class variations. In essence, as a device poses more risk, exposure or consequences to the healthcare professional and the patient, the higher the classification and the more rigorous the standards are to assure public safety. NKC’s Huygens™ Catheter technology should fall under the FDA Class IIa category but final determination is made by the Notified Body.
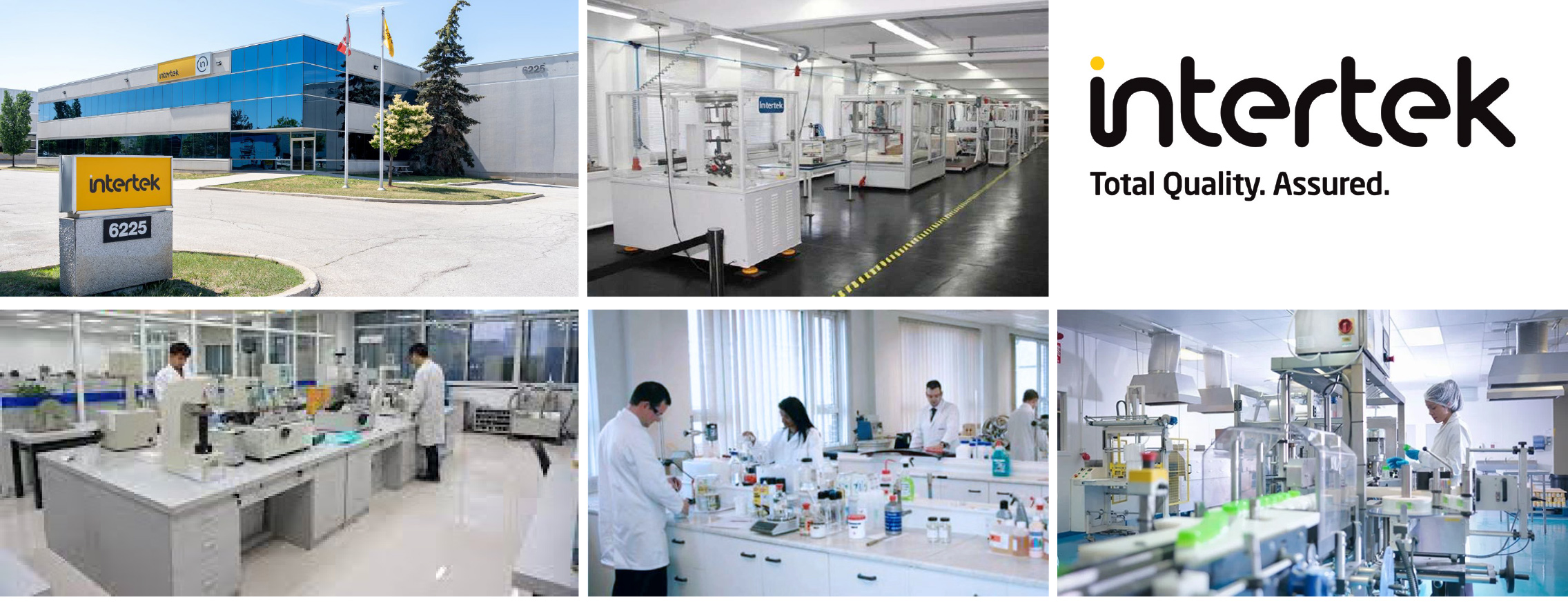
PREPARE FOR INTERTEK SAFETY CERTIFICATION
Along with the data to be developed during the non-GLP Animal Study, NKC will also be working to acquire the Electro-Mechanical Compliance (EMC) validation needed for the FDA submission. To do this, NKC will be working with its partner Intertek to evaluate the Huygens™ Catheter to confirm the device meets all the requirements for an ISO 60601-1 certification. ISO 60601.1 is the technical standard that medical device electrical equipment must meet to be considered safe and effective before they go to market. Developed in collaboration with the International Electrotechnical Commission (IEC), the ISO 60601.1 sets the framework for safety and performance requirements applicable to a wide range of medical electrical equipment. The standard addresses various aspects, including electrical safety, mechanical safety, radiation safety, and software safety as it applies to several key points including:
- Scope and Normative References: Defines the scope of the standard and references other relevant international standards applicable to medical electrical equipment.
- Terms and Definitions: Provides a comprehensive list of terms and definitions specific to the standard, ensuring a common understanding of terminology.
- General Requirements: Outlines general safety requirements that apply to medical electrical equipment, covering aspects such as risk management, essential performance, and environmental considerations.
- Protection Against Electric Shock: Addresses measures to protect patients and operators from electric shock hazards, specifying requirements for insulation, grounding, and other safety features.
- Protection Against Mechanical Hazards: Defines requirements to ensure the mechanical safety of medical electrical equipment, covering aspects such as construction, enclosure design, and protection against moving parts.
- Protection Against Radiation Hazards: Specifies requirements related to protection against radiation hazards, including X-rays and other forms of radiation emitted by medical electrical equipment.
- Protection Against Excessive Temperatures and Other Hazards: Covers requirements to prevent excessive temperatures and other hazards associated with medical electrical equipment.
- Software Safety: Addresses the safety of software used in medical electrical equipment, including requirements for verification, validation, and maintenance.
- Essential Performance: Defines essential performance criteria for medical electrical equipment, ensuring that the device performs its intended function safely and effectively.
Compliance with ISO 60601-1 is essential for manufacturers of medical electrical equipment to ensure the safety and performance of their products, meet regulatory requirements, and facilitate market access for their devices. To this end, Intertek will be performing a conformity assessment of the Huygens™ Catheter to demonstrate compliance with these standards.
Intertek is a global leader in providing safety and performance certification analysis for a variety of manufacturing industries including medical devices. The company was founded in 1888 and has grown to become the largest tester of consumer goods in the world. Intertek has a network of more than 1,000 laboratories across around 100 countries and employs more than 44,000 across 100 countries in over 1,000 locations including large-scale offices and testing facilities in New York City, London, and Hong Kong.
The NKC Engineering team is now working on finalizing all in-house testing of the various electronic components of the Huygens™ Catheter and Huygens™ Catheter Handle to confirm readiness for the study. To date, the team has been able to certify the functionality of the handle board, the communication capability between the handle board and the proximal FCB, and the ability of the distal FCB to measure both biopotential and bioimpedance measurements. Currently, testing of signal processing and Analog-to-Digital conversion in the proximal FCB is in progress and is anticipated to be completed by the end of this month.
All documentation and prototypes to be used in the EMC compliance assessment are scheduled to be completed by the end of Q1/24 at which point Intertek will begin its validation study. The analysis is anticipated to take 30 to 60 days to complete at which point the ISO-60601-1 should be granted.
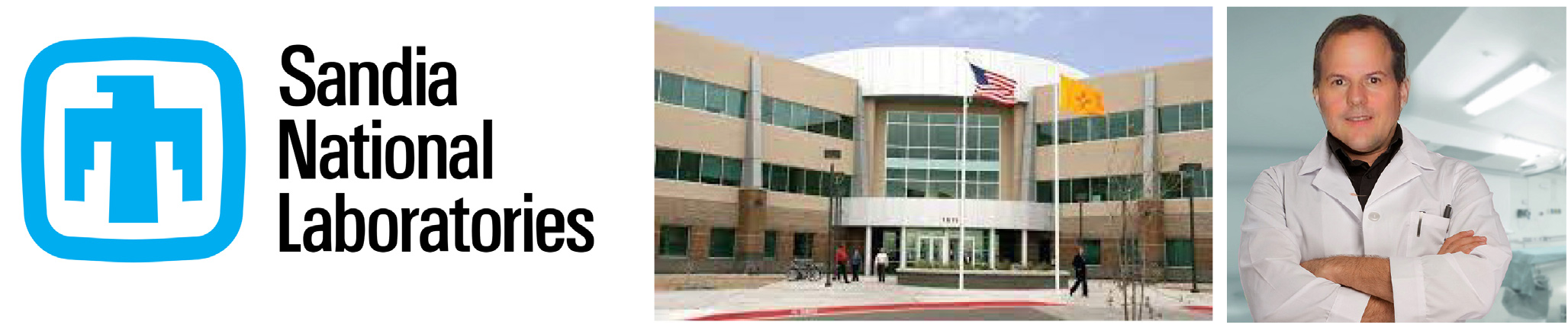
PREPARE ALL MATERIALS AND DOCUMENTATION SANDIA NATIONAL LAB STUDY
NKC has been working with Sandia National Labs since August of 2022 to be its partner in conducting all the validation studies required to confirm the Huygens™ Catheter technology’s ability to capture, process, and display bioelectrical signals to not only the current industry standards but also to the range and resolution that NKC is hoping to achieve with the catheter.
Sandia is one of only three advanced research and development laboratories governed by the U.S. National Nuclear Security Administration (NNSA). Though its primary mission remains to maintain the reliability and surety of nuclear weapon systems and conduct research and development in arms control and nonproliferation technologies, Sandia is recognized as one of the nation’s most trusted facilities for the study and certification of technologies and processes related to computational biology, mathematics, and materials science applications. Validation certification from Sandia is considered to be one of the gold-standard pillars in gaining regulatory license from governing bodies such as the FDA in order to move onto human clinical trials and ultimately gain green-light approval for commercialization.
The NKC studies are being done under the direction of Dr. Darren W. Branch, PhD at Sandia’s National Technology & Engineering Solutions Division. Dr. Branch is one of Sandia’s top research scientists specializing in micro and nanosystems for chemical and biological analysis as well as bio-sensing, neurological interfaces, and adaptive biological interfaces.
Phase I of the testing took place in 2023 where the Huygens™ Catheter was tested to see if it could accurately and consistently capture an array of electrical signals at all the levels of the dynamic range for a standard mapping catheter as well as the lower range ability specific to the Huygens™ Catheter. Testing of this capture was done by first calibrating the Huygens™ Catheter and a standard EP catheter to a U.S. Primary Standard of 1 microvolt which guaranteed that any reading subsequently measured by the Huygens™ and the standard catheter catheters will have no clinically significant error variation between them.
During the initial Phase 1 study, Sandia worked with the Huygens™ Test Board and was able to confirm that the Huygens™ Catheter was able to capture and display the generated signals. For the next study, Sandia will be working with an actual prototype catheter to determine if it can capture and display a simulated QRS signal, The QRS signal is a measurement of the changing direction of the electrical stimulus as it passes through the heart’s conduction system. It is the spikes one sees when looking at an electrocardiogram. The QRS wave is the basis for automatic recognition of heart rate and also as an access point for classification schemes and ECG data-compression algorithms. The QRS complex morphology describes the mechanical action of the heart and provides a view into how each chamber functions by showing the waves of depolarization extending all the way through the heart via each cardiac cycle to produce electrical impulses.
Certification of this ability from Sandia National Labs will provide substantial weight to the FDA when it determines the validity of NKC claims as it seeks 510(k) certification. As with the EMC testing, NKC is looking to complete its in-house testing, prototype procurement, and study documentation by the end of Q1/24 in order to allow Sandia to conduct the next phase of validation testing in Q2.
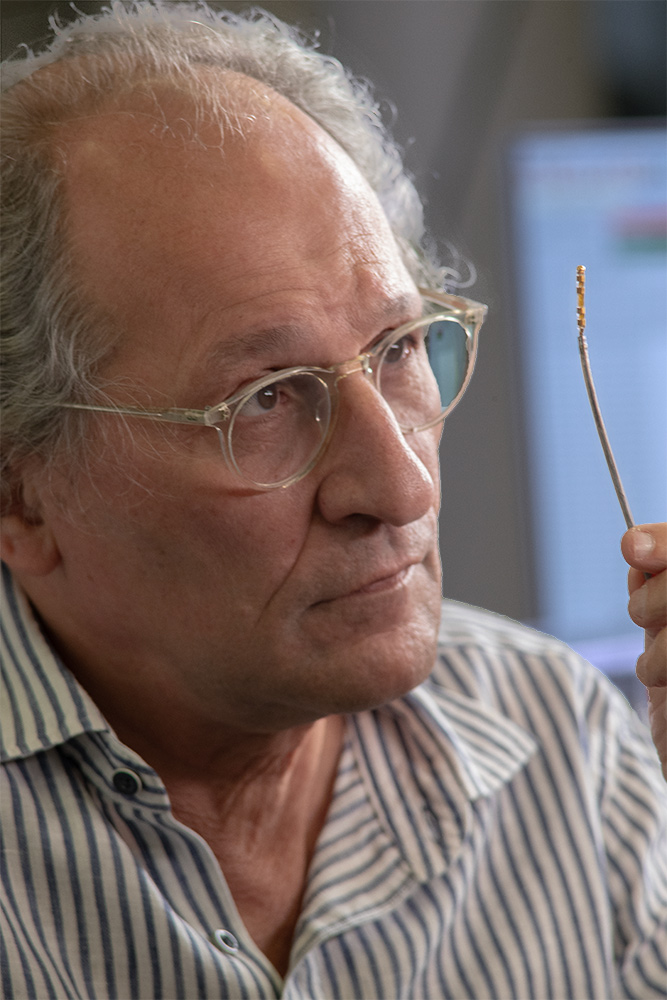
NKC’s CEO Josh Shachar examining the Huygens™ Catheter.
THE ROAD NOT TRAVELED (a reflection)
Robert Frost wrote in his famous poem, “Two roads diverged in a wood, and I took the one less traveled by.” Most people believe this was a metaphor for the personal choice in life between individualism and conformity, between making an easy choice or making the hard decision. It seems at every juncture I have faced in my journey of innovation, my decision was to take the path not traveled. Not to be OK with things as they were, the traveled path, or even the path of just making the less traveled road accessible, but rather to be daring enough to believe there might be a new way of doing something, a better way to get to the destination, whether that be in drug delivery, disease detection, or with NKC, the ability to better diagnose and treat a serious problem which has remained on a more traveled path for too long. In making the decision to forge a new path, one quickly discovers how difficult the journey can be without the help of others willing to help you pave the way. People not afraid to see the potential of unlocking a new solution, of facing the hills and boulders that await you around every corner of progress you make. But with their help, the impossible becomes possible, and the unseen path becomes a new frontier. As I reflect on the journey thus far and can hold in my hands what was once just a dream, but now with the help and efforts of so many, has become reality, I am humbled and grateful to each and every one of those who have stood with me and said, “Let’s walk together and be the explorers who uncover a new future for others to follow.” Thanks to each and every one of you.
– Josh Shachar
NKC CEO and CTO
SAFE HARBOR DECLARATION
THE STATEMENTS, PROJECTIONS AND ESTIMATES OF FUTURE PERFORMANCE OF THE COMPANY OR VARIOUS ELEMENTS OF THE COMPANY’S BUSINESS CONTAINED IN THIS MEMORANDUM THAT ARE NOT HISTORICAL FACTS ARE FORWARD-LOOKING STATEMENTS. INVESTORS SHOULD EXPECT THAT ANTICIPATED EVENTS AND CIRCUMSTANCES MAY NOT OCCUR, THAT UNANTICIPATED EVENTS AND CIRCUMSTANCES WILL OCCUR, AND THAT ACTUAL RESULTS WILL LIKELY VARY FROM THE FORWARD-LOOKING STATEMENTS. INVESTORS SHOULD BE AWARE THAT A NUMBER OF FACTORS COULD CAUSE THE FORWARD-LOOKING STATEMENTS OR PROJECTIONS CONTAINED IN THIS MEMORANDUM OR OTHERWISE MADE BY OR ON BEHALF OF THE COMPANY TO BE INCORRECT OR TO DIFFER MATERIALLY FROM ACTUAL RESULTS. SUCH FACTORS MAY INCLUDE, WITHOUT LIMITATION, (i) THE ABILITY OF THE COMPANY TO COMPLETE THE DEVELOPMENT OF ITS PRODUCTS IN A TIMELY MANNER, (ii) THE DEMAND FOR AND TIMING OF DEMAND FOR SUCH PRODUCTS, (iii) COMPETITION FROM OTHER PRODUCTS AND COMPANIES, (iv) THE RESULTS OF THE COMPANY’S SAFETY AND EFFICACY STUDIES, (v) THE RESULTS OF THE REGULATORY APPROVAL PROCESS, (vi) THE COMPANY’S SALES AND MARKETING CAPABILITIES, (vii) THE COMPANY’S ABILITY TO SELL ITS PRODUCTS PROFITABLY, (viii) THE ABILITY OF THE COMPANY’S THIRD-PARTY SUPPLIERS TO PROVIDE PRODUCTS AND SERVICES IN A RELIABLE MANNER; (ix) AVAILABILITY OF ADEQUATE DEBT AND EQUITY FINANCING, AND (x) GENERAL BUSINESS AND ECONOMIC CONDITIONS. THESE IMPORTANT FACTORS AND CERTAIN OTHER FACTORS THAT MIGHT AFFECT THE COMPANY’S FINANCIAL AND BUSINESS RESULTS ARE DISCUSSED IN THIS MEMORANDUM UNDER “RISK FACTORS.” THERE CAN BE NO ASSURANCE THAT THE COMPANY WILL BE ABLE TO ANTICIPATE, RESPOND TO OR ADAPT TO CHANGES IN ANY FACTORS AFFECTING THE COMPANY’S BUSINESS AND FINANCIAL RESULTS.